The Cummins East Asia Research and Development Center is a joint venture between Cummins Inc. and Dongfeng Motor Corporation. It is the first Sino-foreign joint venture engine R&D center in China. The R&D center was officially opened in August 2006. The accumulated investment in the five years reached 61 million U.S. dollars, of which the total investment for the second phase of the project was 33 million U.S. dollars. The R & D center uses Cummins globally universal tools, equipment and technical standards, has passed ISO900114001 and 19001 quality, health and safety environment certification, after the completion of the second phase will support the development of all Cummins engines from 2.8 to 19 liters, its products are widely used, Covers markets such as automobiles, construction machinery, generator sets and ship engines.
It is reported that Cummins East Asia Research and Development Center currently has a total of 10 engine test benches, which can support Euro V standards and non-road third-phase emission tests. Heavy-duty horsepower benches can enter Europe, South Korea, Singapore, Russia, Australia, and Brazil. The national emission certification provides a “pass†for Chinese OEMs to enter the international market.
At present, Chinese regulations require heavy-horsepower engines to pass full-stream emission tests. The Cummins East Asia Research Center will build a new heavy-horsepower full-flow emission testing system in 2012 and 2013. The second-phase project will have a total of 22 test benches and will be put into use in the first quarter of next year. By then, Cummins will have Euro VI and non-road phase 4 emissions testing, as well as new energy, noise and vibration, cold start, generator set testing and other industry-leading capabilities, to provide Chinese entry-level OEMs access to high-end markets in Europe and America to provide entry "business cards."
According to the relevant staff, the new energy test room for the second phase of the project can realize research and development from the entire new energy power drive system to components (including motors, battery packs, battery management systems, etc.); the vibration and noise laboratory will have a The gas after-treatment system and engine noise testing capabilities will effectively increase laboratory utilization; the new training room and guest room will provide specialized technical training for joint venture companies, OEMs, customers and distributors.
Cummins East Asia R&D Center is also focusing on its own energy conservation and emission reduction while developing clean power: All 11 new engine test bench dynamometers use AC dynamometers. When the engine is running, the electrical energy generated by the AC dynamometer will be distributed to the power station, which will save 15% of the electrical energy at full load. Engine exhaust heat energy will be recycled to the water heating system, saving natural gas consumption. The second-phase project uses natural light to the maximum extent in architectural design, thereby improving the environment of the bench test area and saving energy. The R&D center has also installed a new water treatment system that uses a waste water separation filter to treat all wastewater in a special way, thereby reducing environmental pollution.
Su Zhiqiang, Cummins Chairman and Chief Executive Officer, said: “The improvement of local research and development capabilities is the foundation of Cummins’s established strategy, 'Developing products that meet the market', and how to emphasize its importance is nothing. With the internationalization of Cummins Accelerating our success depends more and more on the performance of the international market, especially emerging markets such as China, India, and Brazil.†He also emphasized the benefits of R&D capabilities to Chinese customers: “We enjoy the best projects in the world R & D team, they across national borders and work together to ensure that Chinese customers can get faster and better service. The expansion of East Asia R & D center strength will accelerate and improve the process."
Continuous Waste Plastic Pyrolysis Plant
Pyrolysis Plant is used for recycling waste tire, waste plastic, waste rubber to fuel oil. According to the actual situation in every country and district, we developed different models of Batch Pyrolysis Plants for waste tires, rubber and plastic with daily capacity 25-40 tons.
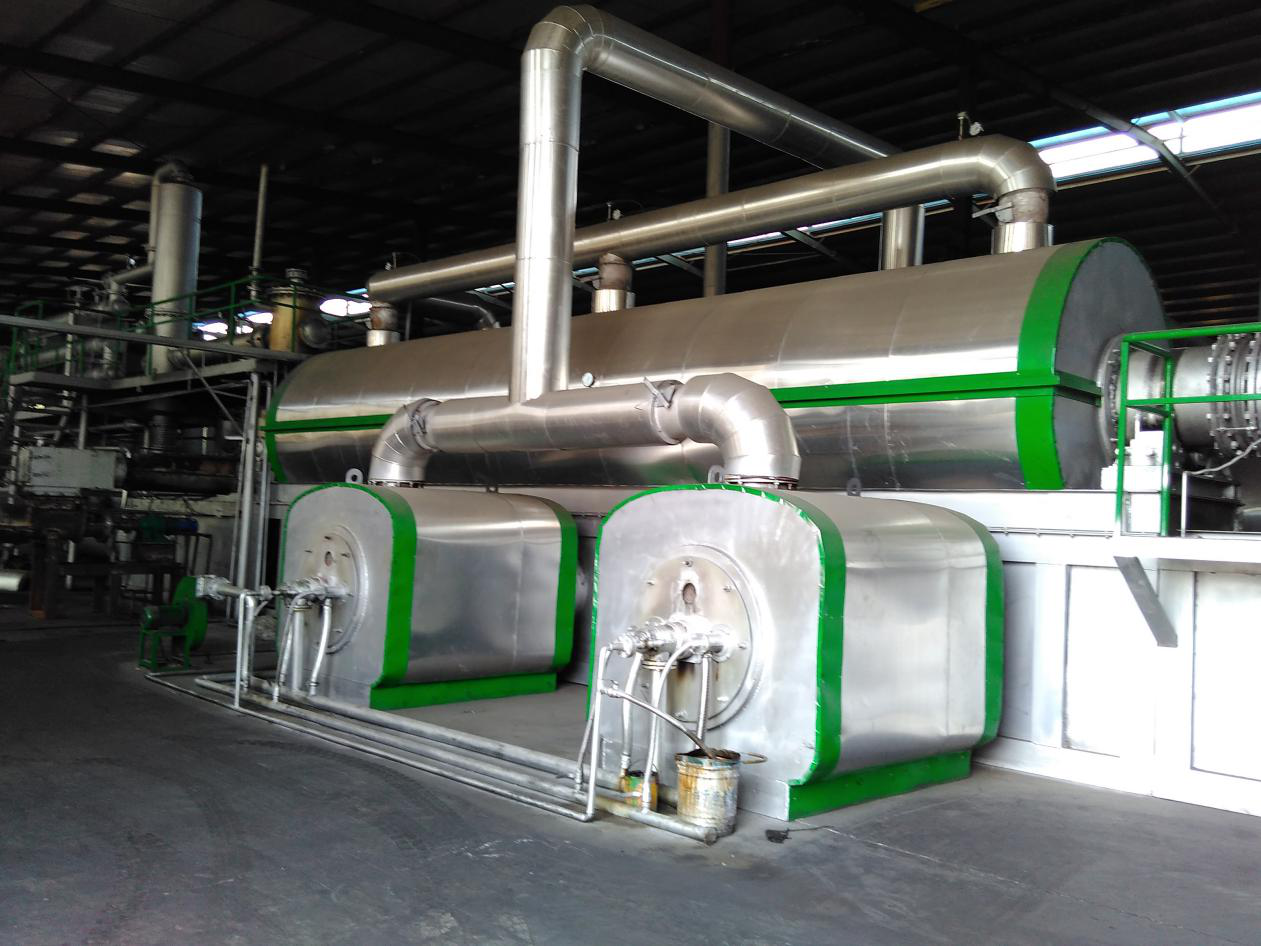
Flow-chat of Continuous Waste Plastic Pyrolysis Plant
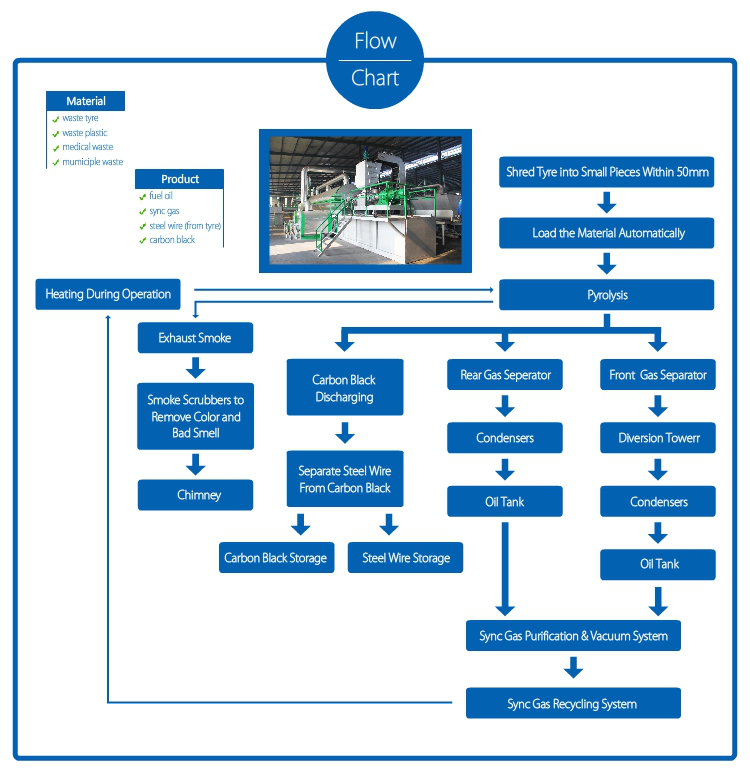
Advantages of Continuous Waste Plastic Pyrolysis Plant
1. Large daily capacity of 25 MT raw materials, and can work 24 hours without any stop for 15-20 days;
2. Auto-loading, auto-discharging and oil coming out at the same time;
3. Only need fuel for the beginning 2-3 hours, then the sync gas generates itself is enough to support heating, saving fuel cost;
4. Low requirement on the raw materials, no need tiny granule, 5cm pieces acceptable for smooth running;
5. High efficiency condensers, more oil output, good quality oil, easy to clean.
6. Sync gas recycling system, fully burned after recycling and utilization, preventing pollution and saving fuel cost.
7. National patent smoke scrubber, can efficient remove the acid gas and dust of the smoke, environmental friendly to meet related national standards.
8. Easy to operate, need less manpower.
Technical Parameter of Continuous Waste Plastic Pyrolysis Plant
NO. |
ITEM |
Technical Parameter |
1 |
Suitable Raw Materials |
Small pieces of Waste tyre,rubber, waste plastic≤5cm |
2 |
Operating Mode |
Fully Continuous Operation |
3 |
Structure |
Horizontal Type Revolve |
4 |
Loading and discharging |
Fully Automatic Feeding and Discharging under High Temperature at Same Time |
5 |
Capacity(24h) |
8-20Mt |
6 |
Work Pressure |
Slightly Negative Pressure |
7 |
Oil Yield of tyres |
40%-45% |
8 |
Reactor Rotational Speed |
1R/M |
9 |
Installation Power |
110kw |
10 |
Cooling Method |
Cycle water |
11 |
Type of Drive |
Sprocket Wheel |
12 |
Heating Method |
Hot Air |
13 |
Noise dB(A) |
≤85 |
14 |
Main Reactor Weight (MT) |
About 20Mt |
15 |
Total Weight(MT) |
About 45Mt |
16 |
Installation Space Required |
60m*20m |
17 |
Manpower |
2/shift |
18 |
Shipment |
5*40HC |
19 |
Delivery time |
≤70Days |
Continuous Waste Plastic Pyrolysis Plant
Continuous Waste Plastic Pyrolysis Plant,Continuous Plastic Pyrolysis Plant,Plastic Pyrolysis Plant
Shangqiu Jinpeng Industrial Co., Ltd. , http://www.recyclingthewaste.com