At present, the low level of automation of domestically produced drying equipment and the backwardness of control means are common problems. As far as the current level of automation is concerned, it is not difficult to solve the control problem in the drying equipment, but what is lacking most is the problem of the reasonable combination of the automatic control technology and the drying equipment. Different materials require different dryers. Similarly, there are major differences in the requirements for control methods for different materials.
As we all know, each drying equipment has its specific scope of application, and each kind of material can find several kinds of drying equipment that can meet the basic requirements, but the most suitable one can only have one kind. If improperly selected, users must not only bear unnecessary one-time high procurement costs, but also pay a heavy price during the entire use period, such as low efficiency, high energy consumption, high operating costs, poor product quality, and even equipment devices. It can't work normally.
The role of automatic control in the dryer is getting bigger and bigger, but its one-time investment is also the issue that people are most concerned about. Sometimes the investment in control equipment even exceeds the investment in the mechanical part of the dryer. It is also the subject that research should be carried out to determine a reasonable control plan for dryers and drying process requirements and to determine appropriate control measures for specific drying projects.
In addition, it should also pay attention to the magnification of drying equipment. The enlargement involves disciplines such as fluid mechanics, mechanics, thermodynamics, heat transfer, materials science, dust removal, corrosion protection, electrical appliances, and control. It is very likely that some problems will arise during the amplification process. Therefore, the amplification of the drying device is by no means a simple geometrical enlargement.
In this respect, it largely depends on the experience of industrialization, the mastery of the physical properties of materials and the understanding of drying equipment. The phenomena that may occur during the enlargement process should be predicted rationally and objectively, and corresponding solutions can be proposed. The so-called research amplification effect is to grasp the drying theory and drying technology while paying attention to accumulating practical experience and summing up lessons.
The development of dryers should also pay attention to energy saving and comprehensive utilization of energy, such as adopting various joint heating methods, transplanting heat pump and heat pipe technology, developing solar dryers, etc., and developing automatic control technology of dryers to ensure optimal operating conditions. In addition, as humans attach importance to environmental protection, improving the environmental protection measures of the dryer to reduce the leakage of dust and exhaust gas will also be the direction that needs further study.
As the quality of equipment, supporting components and basic research still need to be further improved, conventional drying is still the main form of drying. As each kind of drying has its own advantages and application scope, combined drying will be the trend of future development.
Silica, often referred to as "water glass" or "liquid silica," can be used in the preparation of a sizing or primer for canvas that is intended for use with water-based paints or mediums. This is because it has good compatibility with water-based systems and can help to improve the adhesion of paint to the surface of the canvas.
Here's how you might use silica:
1. **Preparation of Silica Solution**: You'll need to prepare a solution of silica. Typically, this involves dissolving silica in water. The concentration of the solution will depend on your specific needs. A common ratio is 2 parts water to 1 part silica, but this can vary.
2. **Application**: Once you have your silica solution ready, you can apply it to your canvas using a brush or spray. The application method will depend on the viscosity of your solution and the type of canvas you're working with.
3. **Drying**: Allow the canvas to dry completely after application. The drying time will depend on the humidity and temperature of your environment. It's important to let it dry fully before proceeding to painting, as any moisture could affect the paint's performance.
4. **Use with Water-Based Paints**: After the sizing/primer has dried, you can then proceed to paint on the canvas using your chosen water-based paints. The silica should provide a good base for the paints to adhere to, improving both the durability and the vibrancy of the colors.
It's worth noting that while silica can be effective in many scenarios, there are other materials that might be more commonly used for this purpose, such as PVA (Polyvinyl Alcohol) or other types of sizing specifically designed for canvas. These alternatives may offer different properties, so your choice should be based on the specific requirements of your project. Always test small areas first when trying out new materials to ensure they meet your expectations.
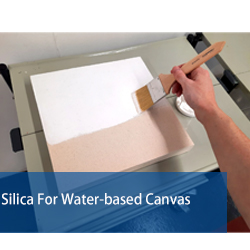
Water Based Primer Agent Silica Dioxide, Canvas Instructure Powder 7631-86-9, Silica Dioxide In Water Based Paint
Guangzhou Quanxu Technology Co Ltd , https://www.inkjetcoating.com