July 15, 2015, the Central gum rubber recycling (Qingdao) Co., Ltd. independent research and development of environmentally friendly ton of waste recycled rubber tire equipment successful trial production. This is the first domestic continuous closed reclaimed rubber production line, and all the indicators have completely met the national environmental protection and energy saving requirements.
China's 10,000-ton waste tire reclaimed rubber equipment has been successfully tested
The company’s general manager, Guo Suyan, introduced that by means of closed and continuous equipment, it is possible to eliminate waste gas, liquid waste, dust, and noise to achieve cleaner production, and to separate personnel, machinery, and materials to achieve the goal of safe production. It is particularly important that this lays the foundation for automation and makes intelligentization possible.
The intelligent program control pre-processing system designed by the company can realize the continuous transportation of raw materials and oil, automatic and accurate measurement, and has the advantages of even mixing and better pre-heated permeability, which provides guarantee for the production of high-quality recycled rubber. In addition, its continuous regeneration equipment adopts a unique flexible self-adaptive spiral structure. In the production process, the spiral can not only scrape off the glue powder adhered on the cylinder wall, but also make the rubber powder adhering to the spiral off by its own axial displacement. Effectively extend the continuous use of equipment.
Wang Yangzuo, former deputy director of the National Environmental Protection Agency, pointed out that the equipment has greatly subverted the current situation of traditional reclaimed rubber production, and achieved full implementation of environmental protection and energy saving goals in terms of the intelligence of raw materials, reagents, and production. The next step should be officially put into production through remodeling or new production lines. .
Aluminum, vacuum-brazed, plate-fin Heat Exchangers can be custom-designed, as every requirement is unique. The cooling way of Heat Exchanger is by air so it's named air-cooled heat exchanger. As the name suggests, air cooled heat exchangers provide a cooling solution for fluids using air which is driven through a fin core by an electrical, hydraulic or mechanically driven fan. Air Cooled Heat Exchangers can be supplied to cool a single fluid, such as engine water, or a combination of fluids as part of a cooling pack which can often include multi fluid circuits cooled by a single fan.
Advantage of Aluminum Air Coolers:
Compact, Lightweight, High Efficient Heat Transfer
Aluminum Core : High strength, high heat conductivity,high safety coefficient.
Supersonic Cleaning: High efficiency,little corrosion to metal , few pollution.
Vacuum Brazing : Strict control of vacuum degree, temperature and time.
Argon Welding : Weld Gaps straight appearance , squamous uniform.
Test : Air tightessn test , Hydraulic Pressure
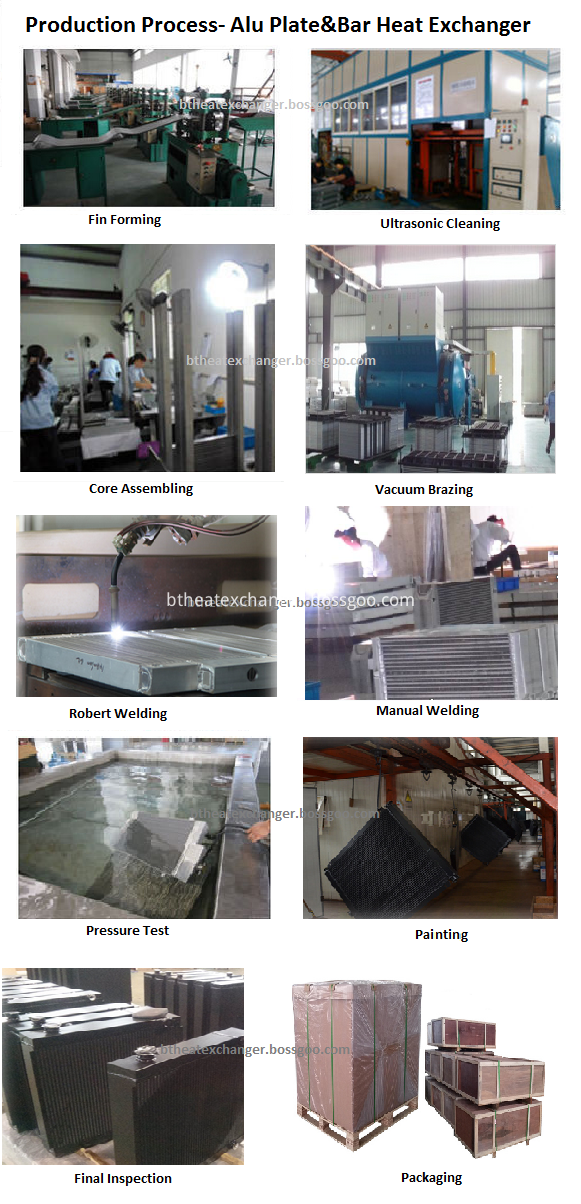
Industrial Air Cooler,Air Separation Plate Fin Heat Exchanger,Air Cooled Heat Exchanger,Aluminum Air Coolers
Wuxi Better Technology Co., Ltd , https://www.btheatexchanger.com